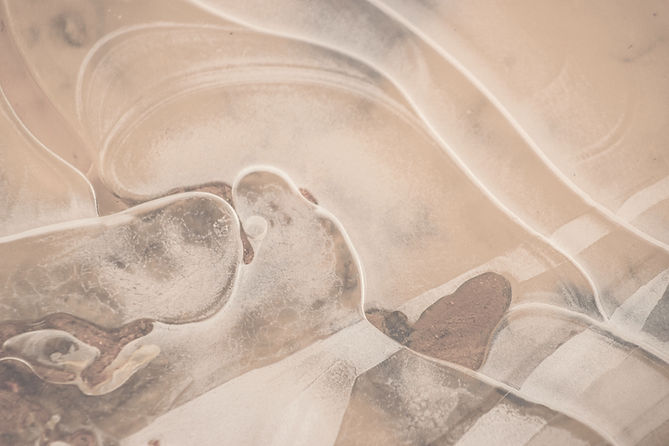
Previous Projects
Emulsion Based Block Copolymers

Upon completion of graduate school, I joined the corporate rotation program at Rohm and Haas. In this role, I ran an exploratory program for CCT derived (meth)acrylic block copolymers. I developed a scalable emulsion polymerization process for the synthesis of a wide range of (meth)acrylic block copolymers of varying architectures (e.g., AB, ABA, star types) and composition. I networked within Rohm and Haas’s Coatings, Adhesives and Sealants, Electronics Materials, and Plastics Additives Divisions to screen various architectures/compositions useful for rheology modification, reactive hot melts, photoresist materials (low PDI polymers), and heat distortion additives for PVC.
Novel Impact Modifiers
I was also a key technical leader in the development of a novel process for making unique thermoplastic impact modifiers that resulted in significant sales growth for Rohm and Haas’s Plastics Additives Division. Furthermore, this was effectively scaled up in North America, Europe, and Asia, being three significantly different manufacturing assets. The process was sufficiently robust that it could fit into the individual unique reactor/isolation/dryer equipment. US2006/0122327 “Process for Preparing Enlarged Latex Particles”
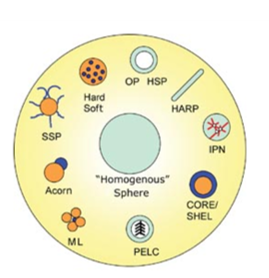

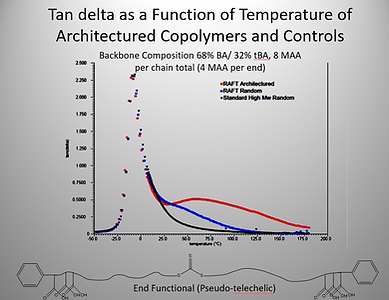

High Solids Solvent PSAs: Controlled Radical Polymerization
Upon transitioning to employment at Avery Dennison Performance Films, I worked as the Emerging Technology Leader where I developed key technology platforms for pressure sensitive adhesives. The technology platforms included emulsion, solution, and solventless free radical polymerization and formulation of the resulting products into pressure sensitive adhesives used in labels, tapes, graphics, and other specialty PSA laminate materials. I led the team to pioneer the commercialization of acrylic pressure sensitive adhesives based on controlled free-radical polymerization. The first commercial application of this novel technology was to dramatically increase the solids content of specialty solvent-based PSAs which lowered costs, increased reactor throughput, reduced carbon footprint, and substantially sped up coating line-speeds. The increased line-speeds enabled additional machine capacity that allowed for growth in very profitable specialty segments without the need for capital expansion. These benefits were achieved, but it was also discovered that PSA formulas could be made with architectured acrylic polymers that exceeded the balance of properties afforded by comparable PSAs made by standard free radical techniques.
US 11,117,994 B2, “Controlled Architecture Polymers”
US 11,034,787 B2, “Acrylic Polymers Having Controlled Placement of Functional Groups”
US 10,266,632 B2, “Ordered Architectures in Acrylic Polymers”
US 10,100,233 B2, “Pressure Sensitive Adhesives”
US 9,550,927 B2, “Acrylic Block Copolymers
“High solids solution acrylics: Controlled architecture hybrid cross-linking pressure sensitive adhesives” PSTC Tech 33, Las Vegas, NV, May 2010.
“Acrylic Pressure Sensitive Adhesives having Controlled Placement of Functional Groups” PSTC Tech 32, Orlando, FL, May 2009 (Dalquist Award Winning Paper/Presentation)
New Tackifiers/Plasticizers
During my time at Eastman Chemical Company’s Adhesive and Plasticizer business unit I developed processes using catalytic chain transfer (CCT) free radical polymerization to make novel (meth)acrylic tackifiers/plasticizers/polymers. Throughout my years in the adhesives industry there has consistently been a lack of weatherable/stable tackifier /plasticizer /processing aids for more polar and durable polymer systems, including acrylic polymers, aliphatic polyurethanes, and aliphatic copolyesters. This was a noticeably clear gap in the product portfolio, and I explored various means of synthesizing these kinds of materials. I successfully made (meth)acrylic tackifiers that were molecularly miscible with a wide range of common high volume acrylic PSAs that yielded classic tackification response. Moreover, specific (meth)acrylic tackifiers in combination with the appropriate acrylic PSA yielded enhanced balance of performance regarding tack, peel, adhesion to low surface energy plastics and shear/temperature resistance. I led a team to do customer discovery, fully develop the value proposition of the material(s), segment customers, engage with target accounts, and scale up the original product. The initial prototype product was scaled up successfully, internal manufacturing assets and tollers were identified, and customers were sampled from a pilot scale.
WO 2018/009683 A1, “(Meth)acrylic Oligomers”

Performance Films Product Development
As a Project/Technical Lead on multiple projects I successfully developed solutions contributed multi-millions of dollars in annual revenue and gross profits. Specifically I led the development of adhesive technologies that enabled next generation Paint Protection Film products that enhanced the speed and quality of installations on cars which is highly valued by the installers and their customers.

Led the technical team for the development of a new dry apply polyurethane based Protective Wrap Film . Protective Wrap Film is a product that serves as a color change film like traditional PVC based wraps with the protection of a clear paint protection film. In addition to the functions of color change and protection the new product was also designed to be easy for installers to apply to vehicles for quick defect free full car wraps. This new product/processes were launched successfully in early 2024.